Spray drying is a technology used to transform liquids, suspensions or slurry feed into dry powder form using heated gas.
The drying process involves
- Feed preparation: The liquid or slurry feed is prepared and filtered to remove impurities and ensure a consistent feed quality.
- Atomization: The feed is then atomized into small droplets by a spray nozzle or rotary atomizer. The size of the droplets determines the drying rate and final particle size of the powder.
- Drying: The atomized droplets are then exposed to a hot air stream, which removes the moisture content. The temperature and flow rate of the hot air are carefully controlled to optimize the drying process.
- Collection: The dried particles are collected in a dust collection system and can be packaged as a dry powder product.
What is the colume of a spray drying tower?
The volume of a spray drying tower varies depending on the scale of the production and the specific requirements of the process.
For small-scale production, a laboratory-scale spray drying tower can have a volume of a few liters. These units are typically used for R&D and pilot-scale production.
For large-scale production, industrial-scale spray drying towers can have volumes ranging from several hundred liters to several thousand liters. These units are designed to handle high volumes of feed material and are typically used in commercial production.
It's worth noting that the volume of the spray drying tower is not the only factor that determines the production capacity of the process.
Other factors, such as the flow rate of the feed, the size of the spray nozzle, and the temperature and flow rate of the hot air stream, can also impact the production capacity.
What are the advantages of spray drying process?
- It is a quick and efficient method for drying liquids or slurries into a free-flowing powder form.
- The process is suitable for a wide range of feed materials, including solutions, suspensions, and emulsions.
- Applicable for food ingredients, pharmaceuticals, pigments and more.
- The final powder product has a long shelf life and is easily transportable.
- The process is easily scalable, making it suitable for both small and large-scale production.
Spray drying may not be the best choice for certain products.
High temperatures in the process can cause thermal degradation of heat-sensitive ingredients.
Low-viscosity liquids can be difficult to atomize and produce small, uniform droplets.
High-moisture content products need a longer processing time, which may significantly increase costs.
Products with poor flow properties can be difficult to handle and process.
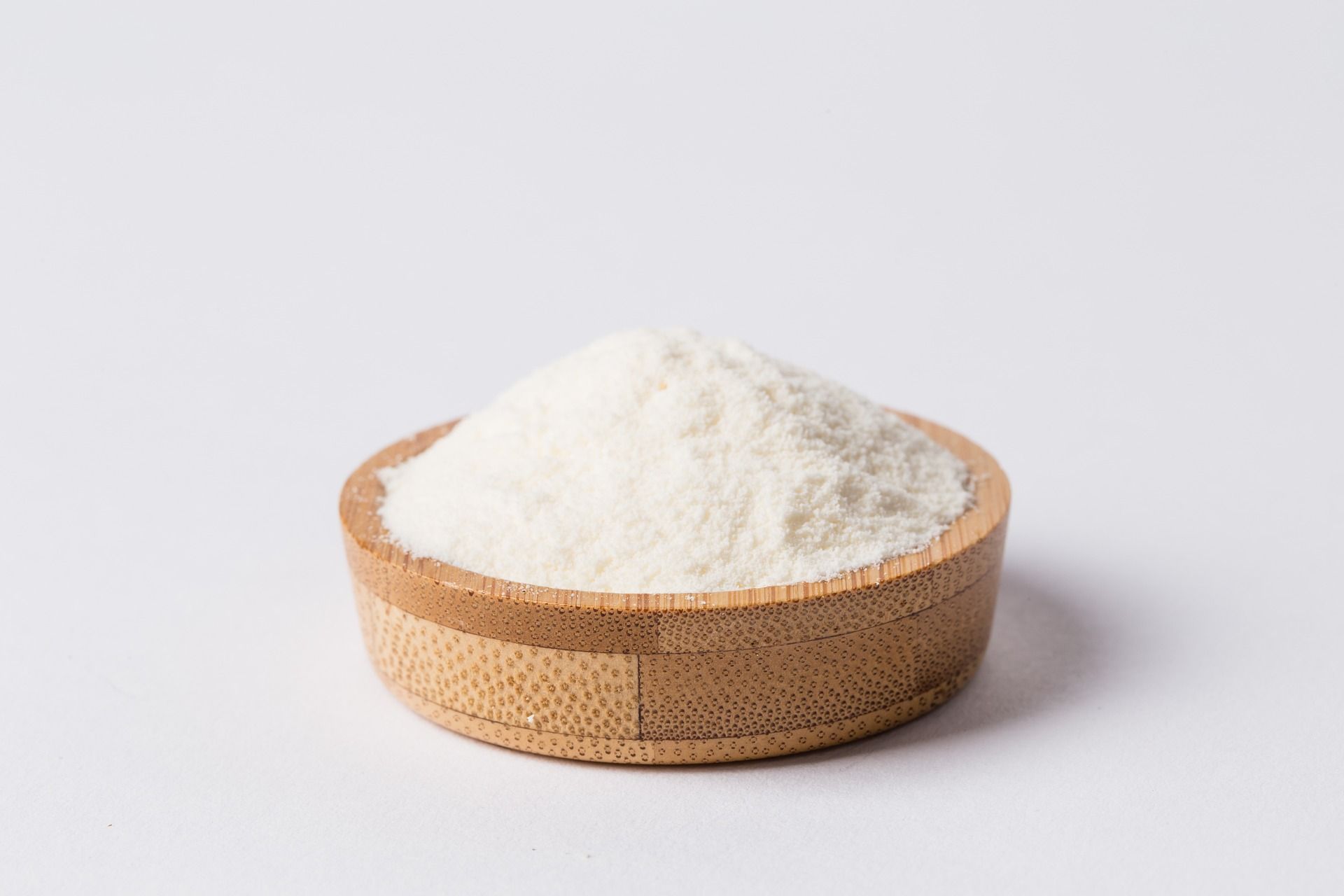
Spray drying applications
Food: milk powder, coffee, tea, eggs, cereal, spices, flavorings, blood, starch and starch derivatives, vitamins, enzymes, stevia, nutracutical, colourings, animal feed, etc.
Pharmaceutical: antibiotics, medical ingredients, additives
Industrial: paint pigments, ceramic materials, catalyst supports, microalgae
How can you make the process more efficient?
Trials are always necessary to determine if spray drying is the best choice for a particular product.
You can also upgrade your technology and drying towers to use less energy for the same process. How? Write to us to receive information you need.
TL;DR
The suitability of spray drying for a specific product will depend on a variety of factors, including the product's composition, desired end product properties, and production requirements.