Last week we were playing with sand. We shook the sieve with our hands and threw away the remaining stones.
The real challenge in the classification process is to achieve:
โ the most accurate possible separation of the feed material
โ a permanently consistent quality and throughput rate.
The specifications are enormously important for further processing.
Excessive deviation from the target values in the classified material can lead to quality losses in your semi-finished or finished products.
In the worst case, trigger expensive downtimes.
In the industrial sieves you need help from so called tapping bodies to make the process faster.
In all systems where the screen bottom is moved mechanically, you can add rubber balls to the screening material. Due to the vibration when hitting the sieve bottom, the trapped particles are released from the openings and clear the sieve.
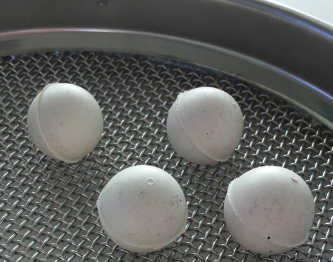
Depending on the processed material and the desired particle size you can use different types & sizes of balls:
rubber, silicone, polyurethane, with solid core, with iron core, magnetizable balls, ceramic, stainless steel, etc.
Further step in the classification process is the analysis.
This is represented as a ๐ฃ๐ฎ๐ฟ๐๐ถ๐ฐ๐น๐ฒ ๐ฆ๐ถ๐๐ฒ ๐๐ถ๐๐๐ฟ๐ถ๐ฏ๐๐๐ถ๐ผ๐ป diagram.
You can enter the required PSD of your material under "Additional Material Info" on the #ProcessOnDemand platform.
This information preselects potential choices and helps the involved partner to estimate whether the material can be produced with the existing equipment.
Have more questions?
Do you agree that the choice of milling balls is crucial for a good processing result?