That’s an interesting term, because it involves the idea of making something bigger instead of smaller. As kids we all loved air balloons. Small rubber bags that you blow up with air or in some cases filled up with water. That was always great fun. And I asked myself: “Are there any processes that make it possible to turn one single particle into a larger one?” And the disappointing answer was: No, it isn’t possible. You can’t pump it up!
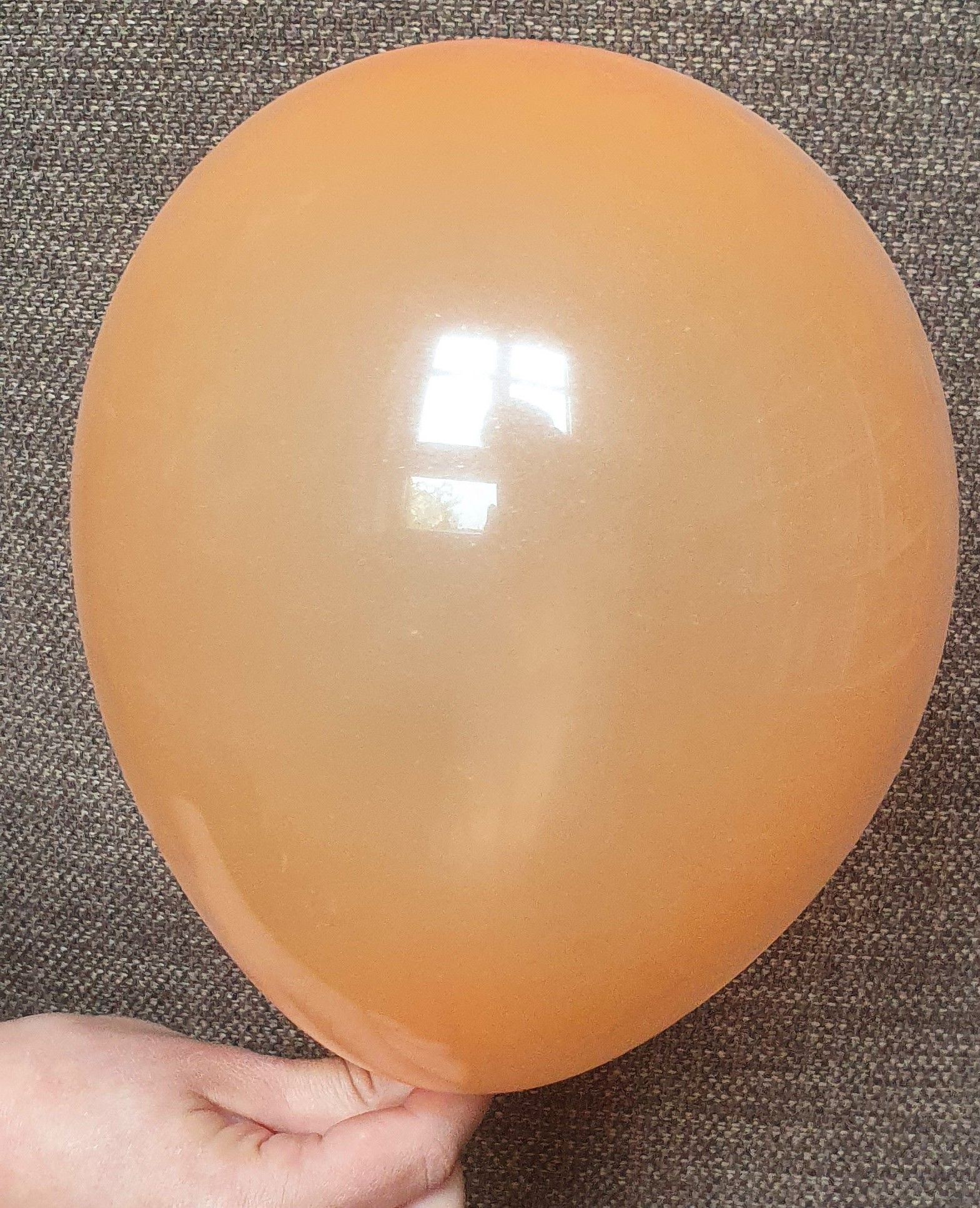
What else is meant by particle size enlargement?
To figure this out it is helpful to look at similar technical terms: granulation, pelletizing, layering, compaction, extrusion or briquetting. Behind these terms is a common principle. Many small particles were connected into a larger unit. And that is exactly what particle size enlargement means in industrial processes. It’s defined as a specific enlargement process in which particles are "glued" together to form larger units, e.g. turning coal dust into charcoal briquettes.
Why do you want to make something bigger when you have previously put so much effort, time and money into making something small?
The answer is not that difficult. By enlarging, certain unwanted effects could be eliminated or in other words certain wanted effects can be designed. If you like baking chocolate cakes you know there is the point to put some cacao powder into the butter. But why don’t you put the same cacao powder with some sugar into your milk to drink a cup of hot chocolate? The answer is as easy as clear: It doesn't dissolve in the milk as well as specially made cacao powder does. It also doesn’t taste as nice and creamy. It tastes rather clumpy and unfamiliar. How can it be, when the ingredients are almost the same? With the help of particle size enlargement you can design special product characteristics.
This is the main reason for using this method.
And of course there is one more. Useful products can be made from supposed waste. Anyone who has ever sawn wood knows this. Sawdust or small amounts of wood left over after processing. But these small particles or pieces of wood are not necessarily waste. I would call it valuable material! Through particle size enlargement, wood briquettes or pellets can be produced, or chipboards and similar products.
There are five main aspects to use particle size enlargement:
- Improve flowing properties - Larger products flow much better than smaller, because they have a less surface area to stick on
- Improve dispersibility – Fine powder isn’t able to disperse as good as special designed and enlarged particles material. I have an example for you. Stir a spoonful of flour into a glass of water and compare it with a spoonful of granules for instant tea. What would you see?
- Adjust bulk density – That means to produce units with greater or lesser density exactly as needed
- Dust reduction or improved product appearance – Dust reduction is important and necessary in many cases for health reasons, especially with toxic materials, or simply to reduce the risk of explosions. I will make a simple example from the household. When you make a mixer sugar into powdered sugar an extremely fine cloud of dust comes out of the container. This dust, combined with a high pressure or a spark, can cause a huge explosion.
- Reduce segregation aspects – This is needed to keep a uniform distribution of different ingredients by “gluing” the particles together, e.g. at dishwasher tabs or pharmaceutical substances in tablets.
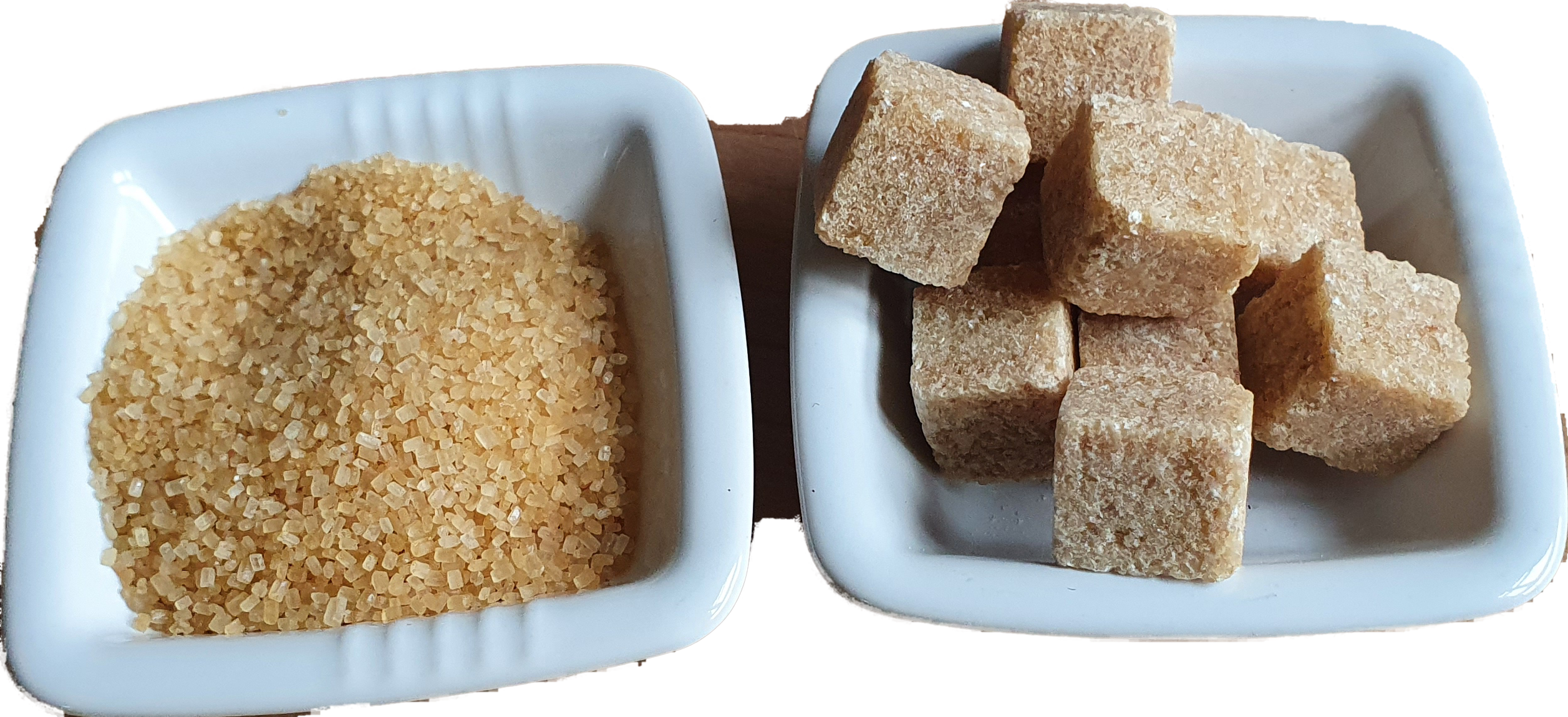
How can we agglomerate particles?
There are 4 four suitable processes for this:
- Pressure - To agglomerate with pressure is almost clear. You have powder or small particles and with the help of high pressure you can form bigger units. The surfaces of the particles interlocked in this step and form a compact solid material. As the charcoal briquettes which are mentioned at the beginning.
- Thermal heating – It is possible to agglomerate with thermal heating when you have at least one material that is meltable. The materials are mixed, heated and cooled at the end. Machines like extruders are often used for this process. It is suitable for many plastics.
- Drying – To agglomerate with drying you insert a wet material into a dryer. The wet particles attract each other during mixing and bond with their surfaces. By drying, the bonded particles form a stable larger unit.
- Wet agitated granulation – To agglomerate with wet agitated granulation method you have to use a special process. The original powder is mixed with a binder and then dried into granules. The main difference between drying is the use of a binder and of course the use of special designed systems.
Yes, even we at Triangular can’t pump up a single particle like a balloon.
What we manage:
- We help you to growth your business.
- We help you to find experts or facilities to produce your material.
- We connect you with the right partners to bring you and your business forward.
You can help a material owner with
- sharing your expertise and
- sharing your production capabilities to manufacture their products and bring them to market successfully.
I believe joining our forces and strenghts, we can provide excellent solutions. It is comparable to particle size enlargement. Creating something big from many small building blocks.
Which products do you agglomarate and which technology do you use?
What are the pros & cons in your opinion?